Mechanical Engineering
Becht is here to bring peace of mind to owners no matter the pressure, temperature or material of their operating equipment. Our fast response team is available 24/7 to evaluate equipment, both new and degraded, and evaluate their adequacy with the latest Industry Codes and Standards. We are here to partner with our clients throughout the lifetime of their equipment, going beyond just analysis to give practical solutions and thereby drive world-class reliability, safety, and profit.
Contact an Expert
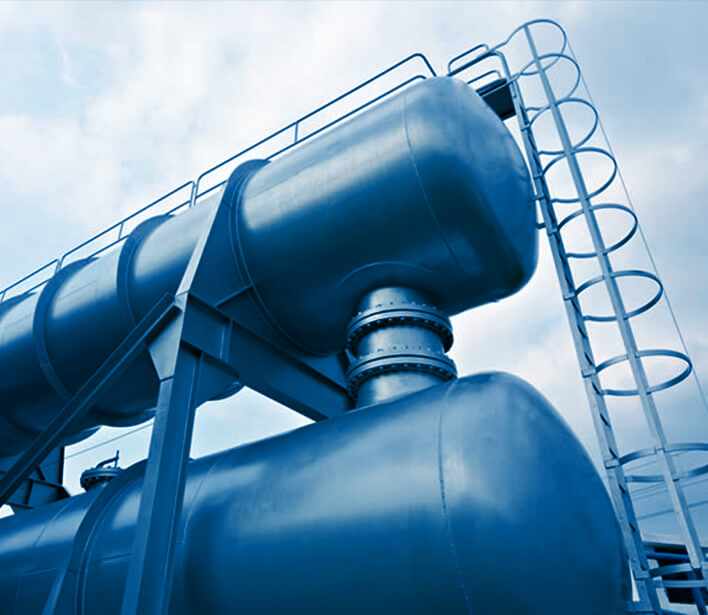
Fitness for Service
Are you worried the damage you just found will force you to shutdown your equipment? Are you tired of spending large chunks of your budget fixing things that were just installed? Do you need to push the envelope on process conditions to get that competitive edge in margin or product quality? Becht is here to provide the right expertise with an owner’s perspective at a moment’s notice.
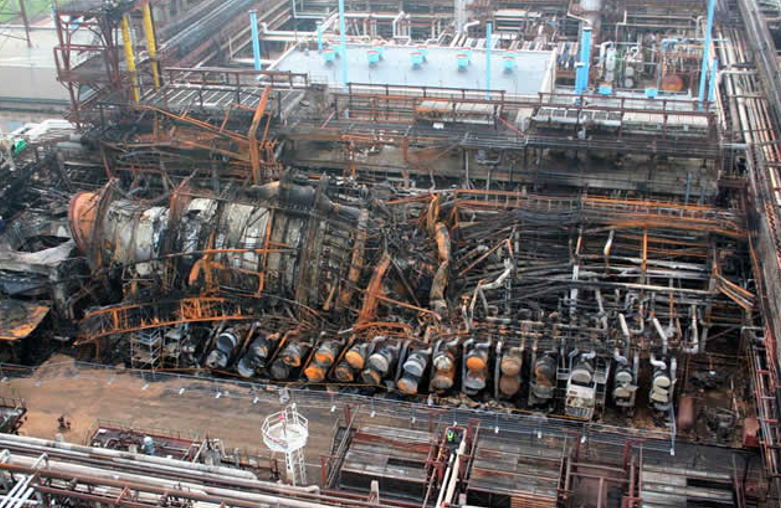
Emergency Support
Unplanned outages, both large and small, can result in significant loss of revenue, pose safety risks, and may render the plant unable to operate for extended periods. Becht takes the guess work out of getting the equipment back up and running as quickly and safely as possible. We leverage creative solutions to avoid long-lead replacements while remaining RAGAGEP (regularly and generally accepted good engineering practices) compliant. Our large staff of experienced engineers with an owner’s perspective address all aspects of any emergency or fire situation. We are ready and able to quickly respond to any emergency and immediately provide practical solutions to get individual equipment or entire units back in service.
Our Emergency Support Services:
- 24-Hour Emergency Support
- On-site Support
- Fire Damage Assessments
- Equipment Failure Assessments
Examples:
Post construction and fitness for service
Discovering corrosion, cracks, bulging, vibration, or other such issues can be unsettling and jeopardize reliability. The correct approach for fixing the issue may not always be apparent at first glance. While establishing fitness-for-service we always look to safely limit lost opportunity production and find the root-cause to provide solutions both in the moment and in the future. We combine unparalleled multidiscipline expertise and depth of in-service knowledge with cutting edge analysis tools to solve challenging issues.
Our rapid response post construction services:
- Fitness for Service
- Equipment Repair
- Equipment Rerating
- Vibration Assessments • Fracture Mechanics
- Elevated Temperature Evaluations
- Metallurgical and Corrosion Evaluations
Examples:
- Fitness for Service (FFS) Analysis for Major Refinery
- Crack Flaw Analysis of Coker Bottom Flange
- Design and Analysis of Steam Injection Piping
- Becht Conducts HTHA and Crack-like Flaw Assessment for Reactor
- Becht Conducts Steam Coil Failure Analysis
- Becht Completes Onsite RCA Support for Client Hydrotreater
- Becht Engineering Supports Oceania Client in Wake of Earthquake
- Computational Fluid Dynamic (CFD) Analysis Resolves Deaerator Cracking
- Pressure Vessel Fitness for Service
- Fitness-For-Service of a Vacuum Tower with Wall Thinning
- Flow Induced Vibration
- Steam Cracking Furnace Repair
- Weld Misalignment
- Vessel Life Assessment
Design
New Construction
New equipment is a major investment for any owner, and it is both frustrating and costly to have newly installed equipment not perform as planned or fail. At Becht, it is our top priority to design new equipment right the first time, every time. Our experienced staff provide world-class technical service and knowledge for new equipment design that saves our clients time and money.
Our industry leading new construction coverage:
- ASME Code Expertise (hyperlink to list)
- Section I
- Section III
- Section VIII
- B31.1
- B31.3
- Etc
- API Code Expertise
- Project Owner’s Engineer (link to project page)
- MDR/UDS certifying Engineer • Tank Design
- Piping Modeling and Stress Analysis
- High-Pressure Design
- Fracture Mechanics
- Elevated Temperature Design
- Bolted Flange
- Vessel Internals
- Structural Support
- Foundation Design
- Pressure Vessel Design
- Heat Exchanger Design
Examples:
Advanced Analysis
Operating units and equipment are becoming more complex and their operating conditions more severe with every passing year. Margins can also be tighter requiring optimized designs and less wasted material. With this increased complexity, severity, and cost restrictions the need for advanced analysis has never been greater. Becht is highly competent in leveraging the most modern and technically sophisticated analysis techniques with a practical, experience-based approach to efficiently resolve complex problem. Our personnel bring world-class technical service and a knowledge of what works and doesn’t work for any of our clients’ analysis needs.
Our cutting-edge advanced analysis services:
- Finite Element Analysis
- Computational Fluid Dynamics
- Heat Transfer
- Fluid Flow Transient
- Fracture Mechanics
- Elevated Temperature Evaluations
Examples:
- Fitness for Service (FFS) Analysis for Major Refinery
- Crack Flaw Analysis of Coker Bottom Flange
- Becht Conducts HTHA and Crack-like Flaw Assessment for Reactor
- Computational Fluid Dynamic (CFD) Analysis Resolves Deaerator Cracking
- Soil-Structure Interaction Analysis of Buried Tanks
- High Temperature Valve Transient FEA
- Deflagration
Equipment Specification & Procedures
Standardizing the requirements for equipment, processes, or fabrication can save significant frustration, time, and money. Let Becht correctly establish the proper considerations and requirements for a successful project from the beginning. Our experience and capabilities are unmatched in knowing what to look for to prevent problems down the road. Our personnel are highly experienced in providing the technical expertise for specification and standards development.
Our World Class Equipment Specification & Procedure Development:
- Pressure Vessel Mechanical Specification
- Fabrication Specifications
- Refractory Specification
- Project Owner’s Engineer (link to project page)
- Weld Procedure and Specification (hyperlink to PONO)
- Process Specification (hyperlink to Process)
Examples: